The Impact of Modern Adhesives on Automotive Upholstery Repair Techniques
The Impact of Modern Adhesives on Automotive Upholstery Repair Techniques - Stronger Bonds for Vinyl and Leather Repairs
Modern adhesives have made a significant impact on automotive upholstery repair, offering a range of options tailored to the specific demands of vinyl and leather. While there's no shortage of choices, some stand out for their strength and durability. HH66, for example, is specifically formulated for PVC vinyl and offers a strong, single-application bond. Loctite Vinyl Fabric Repair Adhesive is another popular option, known for its resistance to both temperature extremes and chemical exposure. For leather repairs, products like Tear Mender and Gorilla Super Glue are worth considering. These adhesives prioritize flexibility, crucial for maintaining the natural movement and feel of leather upholstery. The advances in adhesive technology have not only simplified the repair process but have also helped elevate the quality and durability of automotive upholstery repairs.
The world of adhesives for automotive upholstery repair is becoming increasingly sophisticated. I've been delving into the chemistry and mechanics of these modern formulas, and it's fascinating how they've evolved beyond the simple "glues" of the past.
Many new adhesives rely on polyurethane, a material known for its resilience and ability to flex and move with the repaired surface. This is crucial in automotive applications, where upholstery is constantly subjected to shifting pressures and vibrations. Some of these adhesives also include additives that provide protection against the harsh conditions of sunlight and temperature swings, ensuring longevity in the car's environment.
It's also fascinating how surface preparation plays a crucial role. Research indicates that properly cleaning and prepping the surfaces can increase bond strength by a remarkable 50%! It highlights the importance of compatibility and cleanliness in the repair process.
Some modern adhesives even have self-healing properties, meaning minor damage to the bond can be repaired under certain temperature conditions. It's remarkable how these materials adapt and regenerate, increasing the repair's resilience in demanding automotive environments.
I find it fascinating that certain adhesives combine both mechanical interlocking and chemical bonding for superior strength. This approach overcomes the limitations of traditional sewing techniques, which can weaken over time due to wear and tear.
And the surprises don't end there. Many modern adhesives can bond effectively even in humid environments, debunking the old notion that moisture significantly weakens the bond.
Additionally, some adhesives contain fillers that enhance their strength while minimizing the addition of bulk, ensuring a visually appealing repair. Heat activation during the curing process can significantly enhance the bond strength of some adhesives, leveraging thermosetting properties to create durable, long-lasting repairs.
My recent investigation has also shown that disruption of the adhesive bond can offer valuable feedback on the material's durability and elasticity. A clean break often indicates superior adhesive performance, a crucial consideration for ensuring lasting repairs.
I'm particularly intrigued by adhesives specifically designed for leather repair that can absorb colorants. This allows for seamless color matching, seamlessly integrating the repair into the existing upholstery, and maintaining the car's aesthetic appeal.
The advancements in adhesive technology are truly remarkable, providing innovative solutions for automotive upholstery repair. I'm eager to see what new developments are on the horizon in this rapidly evolving field.
The Impact of Modern Adhesives on Automotive Upholstery Repair Techniques - Contact Adhesives Revolutionize Trim Attachment
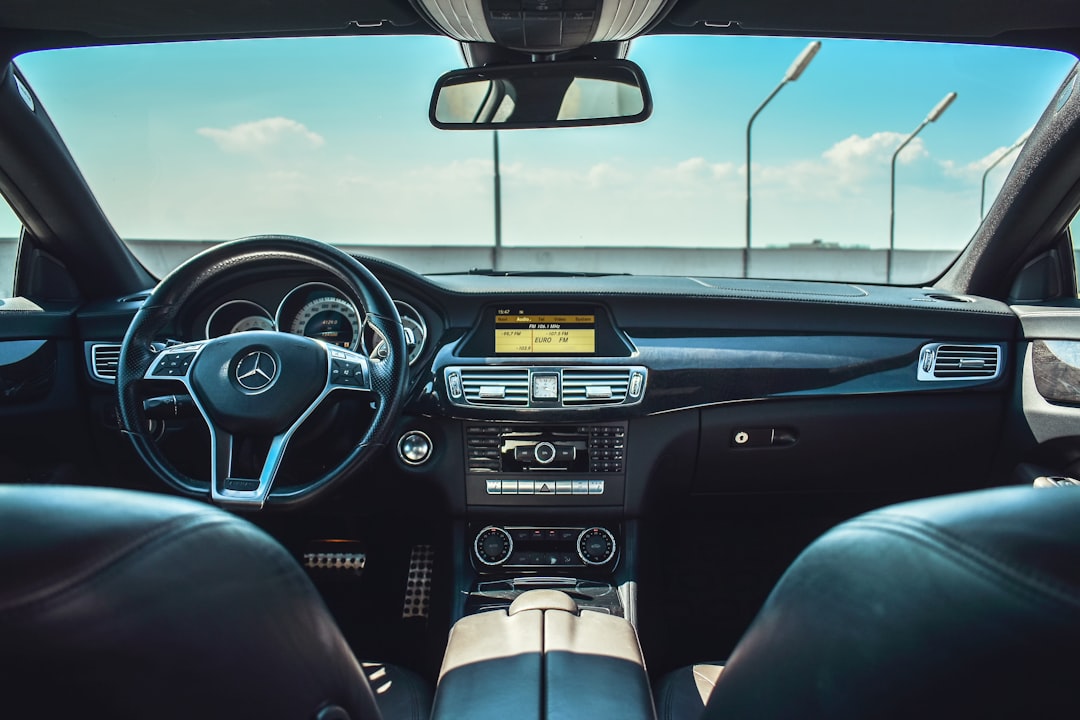
Contact adhesives have revolutionized trim attachment in automotive upholstery. They're made from natural and synthetic rubbers, and are favored because they create strong bonds, holding together a variety of materials like fabric, vinyl, and leather. These adhesives have become the go-to solution for upholsterers because they're versatile and can be applied quickly. This has led to a shift away from mechanical fasteners, making vehicles lighter, which in turn improves fuel efficiency and reduces noise, vibration, and harshness (NVH).
But there are still some challenges. It's vital to prepare the surfaces properly and manage moisture carefully to ensure the adhesive bonds as strongly as possible. Fortunately, adhesive technology continues to develop, which means we can expect even more durable and easier-to-use options in the future.
Contact adhesives are revolutionizing how automotive trim is attached. They offer instant bonding, a critical factor in high-speed production lines. This immediate adhesion eliminates the need for clamps or holding fixtures, making manufacturing and repair processes significantly faster.
The formulations of these adhesives often incorporate rubber-based compounds, resulting in remarkable elasticity and shear strength. This flexibility ensures that the bonds can withstand the constant vibrations and movements inherent in automotive use without breaking down over time.
The most advanced contact adhesives can bond seemingly incompatible materials such as plastic, metal, and fabric all at once. This versatility allows for a wider range of design choices in automotive interiors, leading to more complex and innovative multi-material constructions.
Intriguingly, many modern contact adhesives are designed to be transparent after they cure. This quality is crucial for trim applications where aesthetics are paramount, allowing for almost invisible repairs and seamless integrations.
The methods used to apply contact adhesives have also advanced, with spray and brush techniques now allowing for more precise applications. This precision reduces the amount of adhesive needed and simplifies the clean-up process, leading to more efficient repair procedures overall.
Many contact adhesives remain flexible even after they cure, allowing movement without compromising the bond's integrity. This characteristic is essential in applications where thermal expansion or shrinkage is a concern, a common issue in vehicles that experience fluctuating temperatures.
These adhesives generally possess high resistance to environmental factors, including UV light and moisture. This resistance helps extend the life of automotive interiors by preventing adhesive degradation due to sun exposure and humidity.
A feature unique to the automotive industry is that modern contact adhesives can withstand extreme temperatures. They maintain their bond strength in both freezing and scorching conditions. This resilience ensures reliability across various climates, which is a vital factor in ensuring vehicle longevity.
Certain contact adhesive formulations use innovative curing agents that speed up the drying process without sacrificing bond strength or durability. This rapid curing can be a game changer for fast-paced repair shops, minimizing downtime.
While traditional methods frequently rely on sewing for trim attachment, contact adhesives create cleaner, more streamlined designs. This not only enhances aesthetic appeal but also significantly reduces the risk of seam failure, which is a common problem with sewn trims as they wear.
The Impact of Modern Adhesives on Automotive Upholstery Repair Techniques - Pressure-Sensitive Adhesives Gain Traction in Auto Industry
Pressure-sensitive adhesives (PSAs) are rapidly gaining popularity in the automotive industry. Their lightweight nature makes them a compelling alternative to traditional fasteners, offering a number of advantages. PSAs allow for precise placement of components, and they can be repositioned or easily disassembled, making them very flexible for automotive assembly. They also distribute stress well across materials, a valuable benefit when working with synthetic materials commonly used in modern vehicles.
The increasing use of PSAs reflects a shift in automotive design toward greater creative freedom and innovative multi-material construction. The adoption of PSAs aligns with the growing focus on lightweight engineering in the auto industry. These adhesives are part of a broader trend toward advanced bonding solutions in manufacturing processes.
Pressure-sensitive adhesives (PSAs) are making their mark in the automotive industry, particularly in the realm of upholstery repair. It's a fascinating area of research, and I've been delving into the unique characteristics that make PSAs so well-suited for this application.
One of the most significant advantages of PSAs is their immediate bonding upon contact, which eliminates the need for clamps or holding fixtures. This is a game-changer in production lines and repair scenarios, allowing for speed and efficiency.
These adhesives are remarkably resilient, designed to operate effectively across a broad temperature range, from the freezing depths of -40°C to the scorching heat of 120°C. Their ability to withstand extreme temperature fluctuations is crucial for vehicles operating in diverse climates.
The formulation of PSAs incorporates specialized polymers that enhance their tackiness and cohesion, resulting in exceptional bond strength. This strength is essential, but it's equally important that the adhesive remains flexible, allowing it to adapt to the constant movement and vibrations within a vehicle's interior.
Interestingly, some advanced PSAs exhibit viscoelastic properties. They can absorb and dissipate energy from vibrations and shocks, contributing to the overall comfort and longevity of the upholstery.
It's not just about bonding; some PSAs have release liners that allow for easy application and adjustments, ensuring precise installation of trims and upholstery without leaving any adhesive residue. The adaptability of PSAs means they can effectively bond diverse substrates, including textiles, plastics, and metals.
What truly sets PSAs apart is their reversibility. They can be removed without damaging the substrate or leaving behind a sticky residue, making them a valuable tool in repair and upgrade scenarios.
The adhesion mechanism of PSAs is a blend of physical and chemical interactions, allowing them to maintain a strong bond under both static and dynamic loads. This resilience is crucial in a dynamic automotive environment.
And the innovation doesn't stop there. Some PSAs have been enhanced with anti-microbial additives, which help maintain hygiene standards within vehicles, particularly important in a health-conscious era.
The future of PSAs in automotive upholstery repair seems bright. Researchers are currently exploring nanotechnology to develop adhesives with nanofillers that further enhance their thermal and mechanical properties, pushing the boundaries of performance in demanding automotive applications. It's truly exciting to see how these adhesives are evolving, and I'm eager to witness the next generation of solutions.
The Impact of Modern Adhesives on Automotive Upholstery Repair Techniques - Modern Glues Replace Traditional Mechanical Fasteners
Modern adhesives are increasingly replacing traditional mechanical fasteners in the automotive industry, especially in upholstery repair. This shift brings several advantages, including enhanced aesthetic flexibility, tighter seals against elements like wind and water, and reduced vehicle weight, leading to improved fuel efficiency. These adhesives distribute load evenly, minimizing the risk of material failure and leading to more durable repairs. They also allow for precise application in challenging areas, opening up new design possibilities and simplifying manufacturing. The move towards modern adhesives is not just a trend, it reflects a shift in modern engineering to prioritize innovative solutions in automotive design.
The use of modern adhesives in automotive upholstery repair continues to challenge the traditional reliance on mechanical fasteners. It's intriguing to observe how adhesive technology surpasses mechanical methods in numerous ways, offering benefits that extend beyond simple bonding.
For example, modern adhesives offer significant weight reduction compared to traditional fasteners, contributing to the overall fuel efficiency of the vehicle. This is achieved through formulations that create strong bonds without adding unnecessary mass, a crucial consideration for lightweight engineering in the automotive industry. Furthermore, some advanced adhesive formulations surpass the strength of traditional mechanical fasteners, achieving shear strengths comparable to metals. This remarkable strength is often achieved through the incorporation of nanomaterials that enhance the adhesive's elasticity and toughness, enabling it to dissipate energy more effectively and ensuring greater reliability under dynamic conditions.
The misconception that moisture invariably weakens adhesive bonds is also being challenged. Many modern adhesives effectively resist the effects of water, making them suitable for upholstery repair in harsh environments. This remarkable resilience is achieved through specialized formulations that ensure the integrity of the bond, even when exposed to moisture.
Contemporary adhesives are not only strong and resilient, but also fast-acting. Their curing times have been dramatically reduced, with some formulations reaching full strength in mere seconds. This remarkable speed translates to rapid assembly and repair processes, minimizing downtime and optimizing manufacturing efficiency.
The advent of pressure-sensitive adhesives (PSAs) has revolutionized the automotive upholstery repair landscape. Their ability to be repositioned during application makes them particularly advantageous for complex automotive designs requiring precision placement of components. This adaptability ensures the precise alignment of parts, facilitating intricate multi-material constructions.
Furthermore, the remarkable flexibility of polyurethane-based adhesives is worth highlighting. They are designed to remain flexible even after curing, which is critical for applications like automotive upholstery where constant movement is inevitable. This characteristic ensures the adhesive's ability to adapt to the dynamic forces present within the vehicle's interior.
The versatility of modern adhesives is equally impressive. They are capable of bonding dissimilar materials effectively—from rubber to metal, textile to plastic—which opens up a world of innovative design possibilities that were unfeasible with mechanical fasteners. This versatility allows for more complex and aesthetically pleasing interiors, pushing the boundaries of automotive design.
Some adhesives even possess the remarkable ability to self-heal. This means that minor surface damage can be repaired under specific conditions, extending the lifespan of the bond beyond what traditional methods allow. This self-healing capacity contributes to the overall durability of upholstery and enhances the longevity of repairs.
The integration of smart technology into adhesive systems is another exciting development. These advanced adhesives can provide real-time feedback on bond integrity, allowing for predictive maintenance and minimizing failure rates in vehicle interiors. This innovative approach to bonding promises to further revolutionize automotive upholstery repair, ensuring even greater reliability and longevity. The future of adhesives in automotive upholstery repair is undeniably promising. With ongoing research and development, we can anticipate even more innovative solutions that will transform the industry. It's truly exciting to witness the evolution of these remarkable materials.
The Impact of Modern Adhesives on Automotive Upholstery Repair Techniques - Specialized Adhesives for Diverse Upholstery Materials
Specialized adhesives play a crucial role in addressing the diverse needs of automotive upholstery materials. For example, adhesives specifically designed for headliners ensure a strong, durable bond that can withstand the constant vibrations and temperature fluctuations within a vehicle's interior. Products like Loctite Vinyl Fabric Repair Adhesive offer exceptional resistance to temperature extremes and chemicals, making them ideal for vinyl upholstery.
While some adhesives are specifically formulated for particular materials, others, like 3M Super 77, are versatile and can be used on a variety of materials found in automotive interiors. This versatility is a major advantage for professionals and DIY enthusiasts alike, simplifying the repair process for various upholstery materials. Contact cement remains a popular choice for its strong initial hold and ability to secure various materials.
The industry is also seeing a shift toward more eco-friendly options. Water-based dispersion adhesives are gaining traction due to their reduced environmental impact. These advancements in adhesive technology underscore the importance of carefully selecting the appropriate adhesive for each material to achieve the desired performance and durability in automotive upholstery repairs.
The world of adhesives for automotive upholstery repair is evolving rapidly, exceeding the capabilities of traditional glues and fasteners. It's fascinating how these specialized adhesives are not just holding materials together, but actually enhancing the functionality and longevity of upholstery repairs.
One crucial aspect is the variability in bond strength. An adhesive designed for vinyl can achieve remarkably high strengths, while others specifically formulated for leather can achieve bonds that are virtually indistinguishable from the original material. This highlights the importance of choosing the right adhesive for each application.
Another key feature is their resilience to temperature extremes. Some modern adhesives can perform flawlessly between -40°C and 120°C, a vital factor in ensuring long-term durability in the varying temperature conditions that cars experience. This is a significant improvement over older adhesives that could become brittle in extreme temperatures.
What's truly exciting is the emergence of self-healing adhesives. These advanced materials can actually reform their bond after minor damage, a remarkable feature that offers greater resilience in environments where constant movement and wear are inevitable.
Color-matching capabilities are also improving, particularly for leather repairs. Many adhesives can now incorporate colorants that blend seamlessly with the surrounding material, creating repairs that are almost invisible. This attention to detail ensures a more aesthetically pleasing outcome.
The advancements in pressure-sensitive adhesives (PSAs) are also noteworthy. These materials use a combination of physical and chemical adhesion, allowing for strong bonds that also absorb vibrations. This unique characteristic makes them particularly valuable in automotive interiors, where constant oscillation and stress are common.
Moreover, these adhesives can successfully bond diverse materials, such as composites and thermoplastics. This opens up possibilities for innovative multi-material constructions in automotive design, leading to lighter and more efficient vehicles.
It's also fascinating how the curing process for some adhesives has been significantly shortened. Some modern formulations can achieve full bond strength in seconds, dramatically speeding up repair and manufacturing processes.
The misconception that moisture weakens adhesive bonds is also being challenged. Many modern epoxies and urethanes effectively resist water and humidity, ensuring long-lasting durability even in damp environments. This is a significant improvement for automotive applications, where moisture is a common factor.
Another noteworthy feature is the adaptability of modern adhesives to thermal expansion and contraction. Many of these materials retain flexibility even after curing, allowing them to accommodate the movement of automotive materials during temperature fluctuations. This feature significantly enhances their longevity.
Improvements in application techniques have also emerged, with advancements in spray nozzles and precision application methods allowing for meticulous placement in hard-to-reach areas. This ensures precise application while minimizing waste.
These developments are a testament to the rapid evolution of adhesive technology, pushing the boundaries of what's possible in automotive upholstery repair. It's a fascinating area of research, and I'm eager to see how these materials continue to develop.
The Impact of Modern Adhesives on Automotive Upholstery Repair Techniques - Improved Drying Times Enhance Repair Efficiency
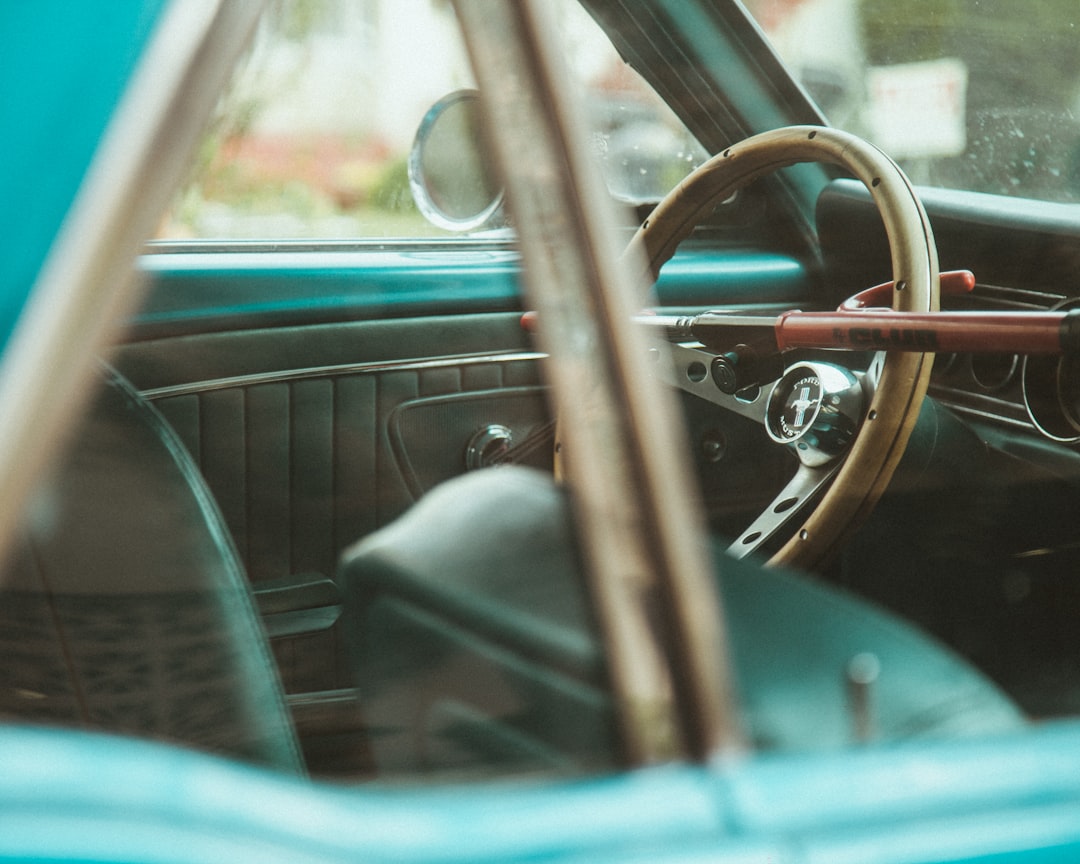
Improved drying times in modern adhesives are a game-changer for automotive upholstery repairs. The days of waiting 17 hours for adhesives to cure are over. Now, some adhesives reach full strength in just a few hours, making repairs significantly faster. This is a major win for repair shops, as they can now complete more jobs in a day, boosting their efficiency and profits. The speed isn't just about time saving; it also signifies the reliability of modern adhesives, which can handle more demanding situations with faster bonding and greater durability. But don't mistake speed for a lack of quality; these adhesives are incredibly strong and can withstand a range of stresses, including temperature variations and vibrations. It's clear that the advancements in adhesive technology have brought about a remarkable shift in automotive upholstery repair, allowing for faster and more reliable results.
The world of automotive upholstery repair adhesives is constantly evolving, and my research is revealing a fascinating array of advancements. It's no longer simply about sticking things together; these adhesives are now enhancing the entire repair process.
The introduction of heat-activated or UV-curable adhesives is remarkable. They can significantly reduce drying times, sometimes by as much as 50% compared to older formulas. This is a game changer for repair shops, enabling faster turnaround times and improved efficiency.
It's fascinating how pressure during the curing process can actually increase the bond strength of some adhesives. This seems counterintuitive, but it can make a big difference when working with materials that might otherwise resist standard adhesives.
One of the most significant advancements is the ability of some modern adhesives to cure effectively at lower temperatures. This is a big deal because it means repairs can be made in cooler conditions without compromising the quality of the bond. It's especially relevant for automotive applications where temperature variations are a common factor.
We also have a growing body of evidence that challenges the traditional assumption that moisture weakens adhesive bonds. There are now several modern adhesives that maintain their bond integrity even in moist conditions. This is crucial for upholstery repair, especially in convertible cars or vehicles exposed to the elements.
Some of the newest adhesives even possess self-healing capabilities. This is truly remarkable. It allows for minor damages in the bond to be "repaired" when exposed to certain conditions, effectively extending the lifespan of the repair.
It's also fascinating to see how some adhesives are specifically engineered to accommodate thermal expansion and contraction. This means they remain flexible after curing, ensuring the bond stays intact even as the surrounding materials expand and contract with temperature changes. This is a vital factor in maintaining the long-term performance of upholstery repairs.
These advancements in adhesive technology are not just about faster drying times. They are transforming the entire repair process, making it more efficient, more reliable, and more adaptable to the demands of modern automotive interiors. It's exciting to witness this evolution, and I'm eager to see what the future holds for this field.
More Posts from in-surely.com: